Garden Office Refurbishment

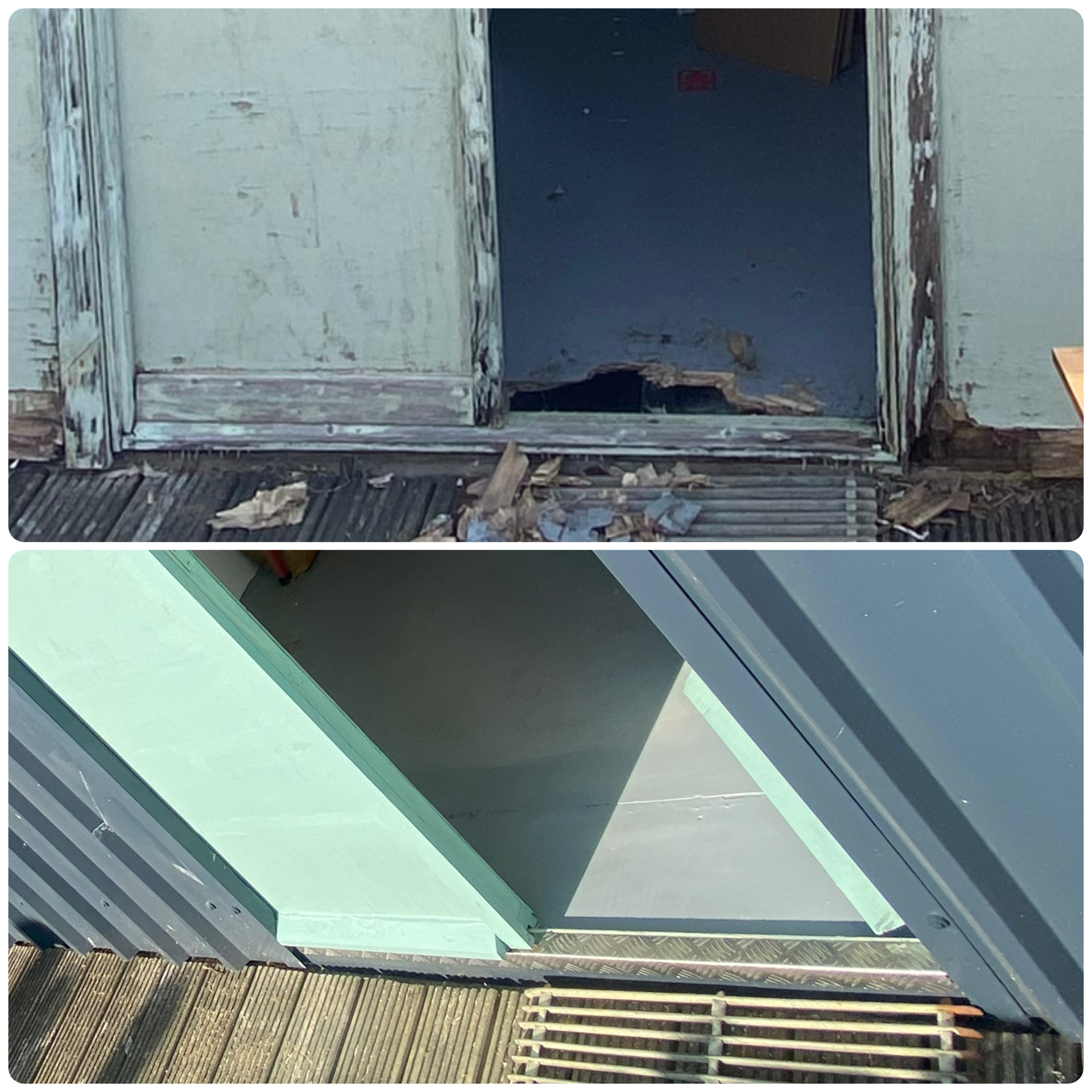
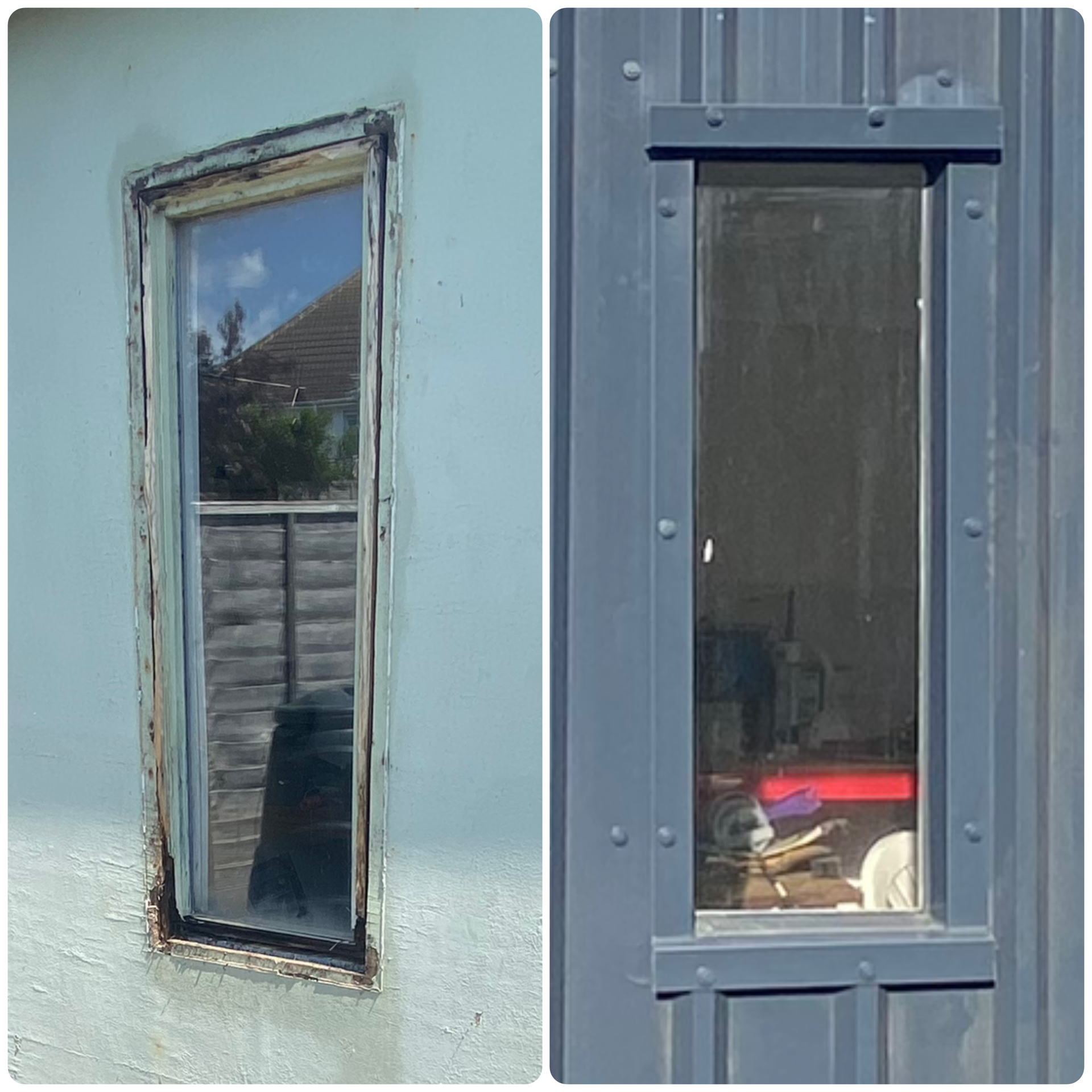

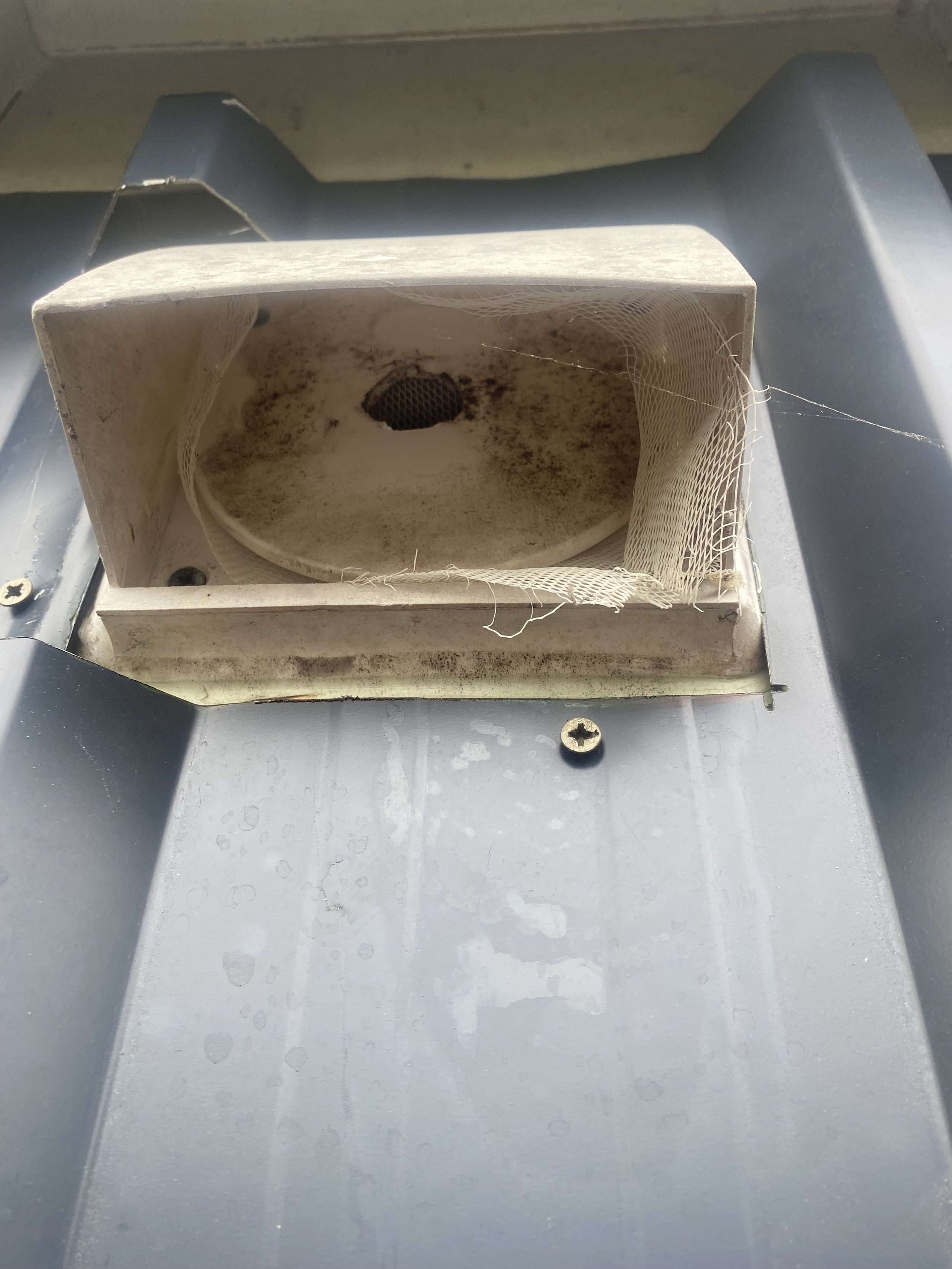
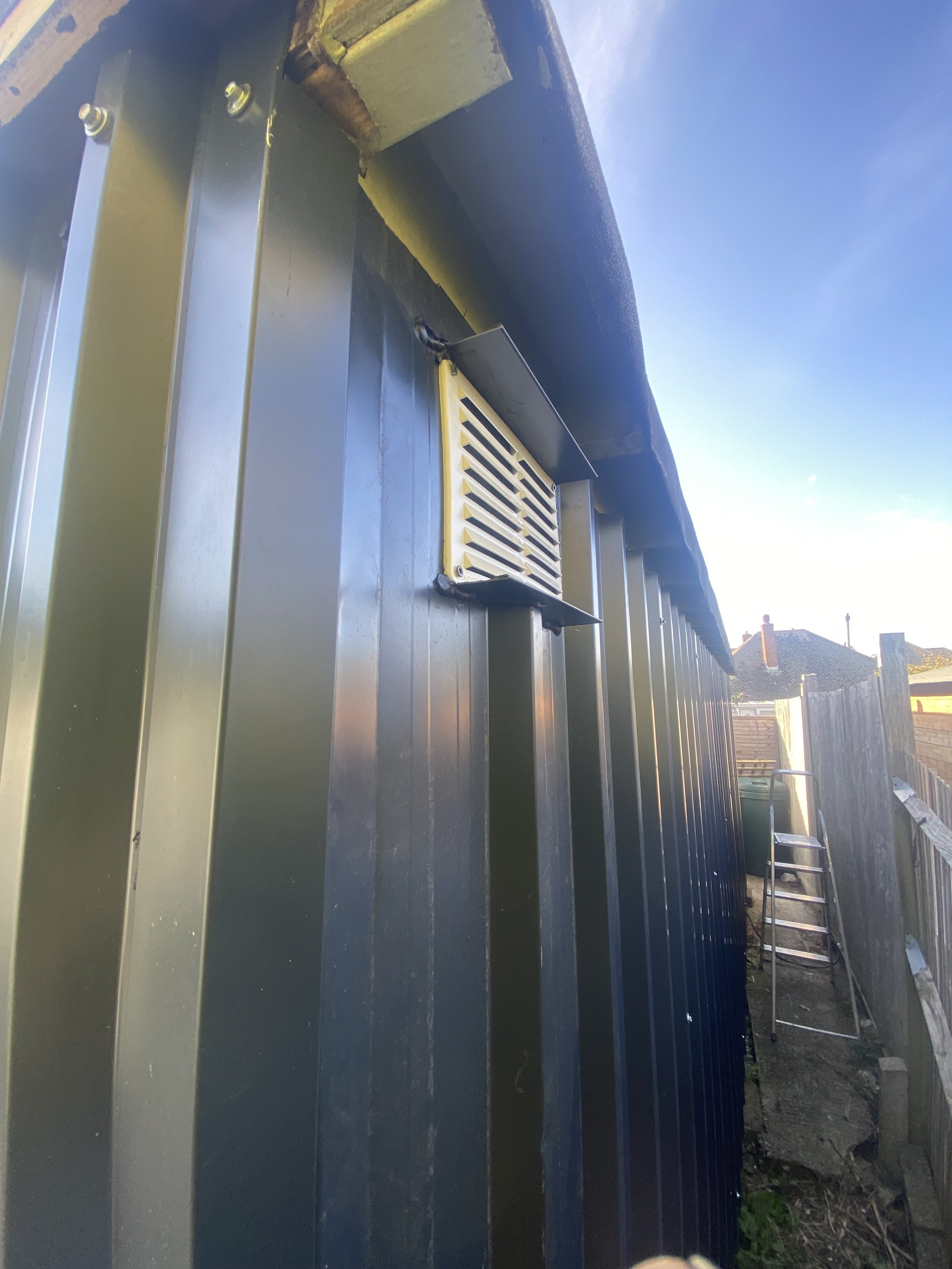
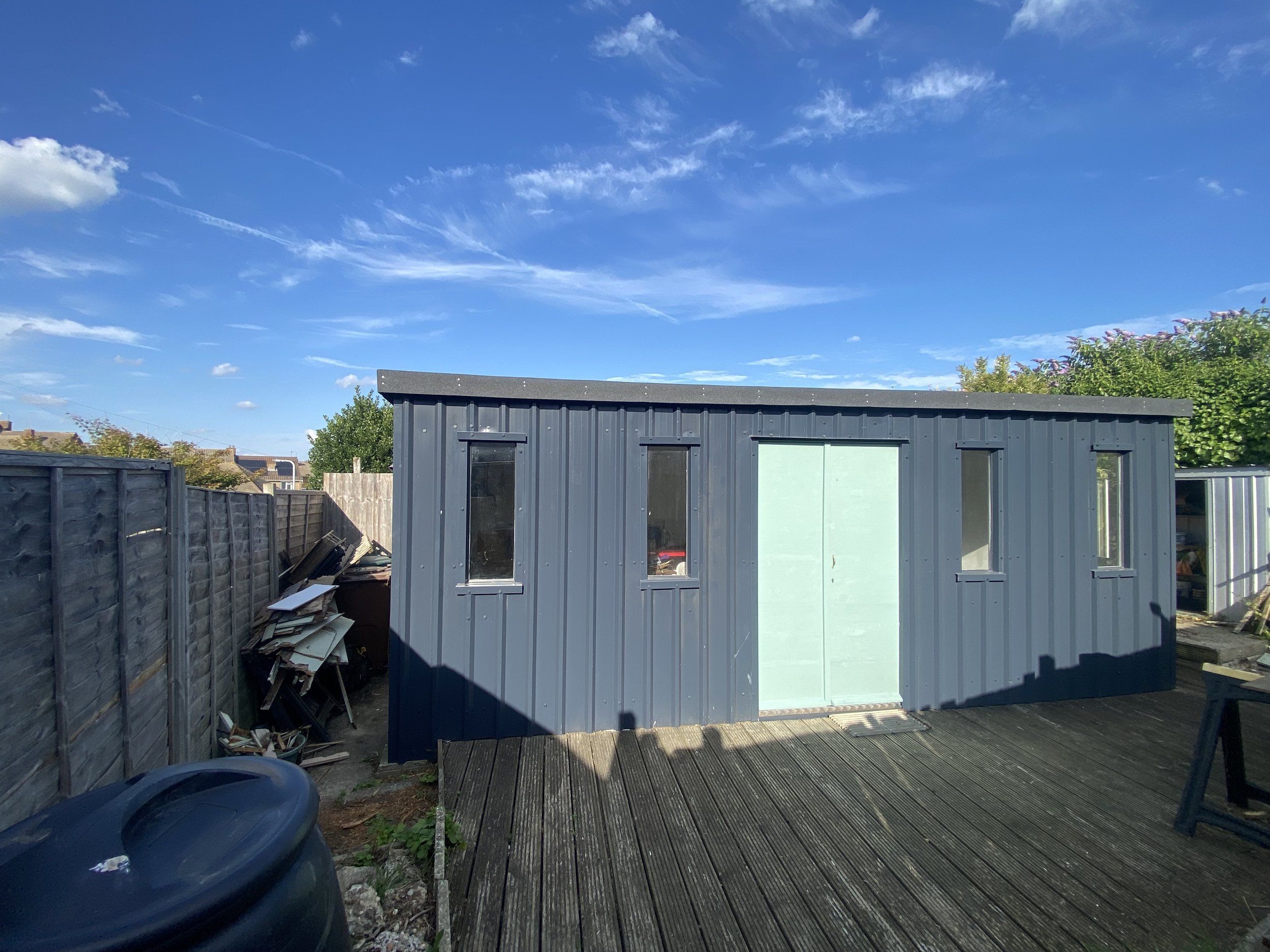
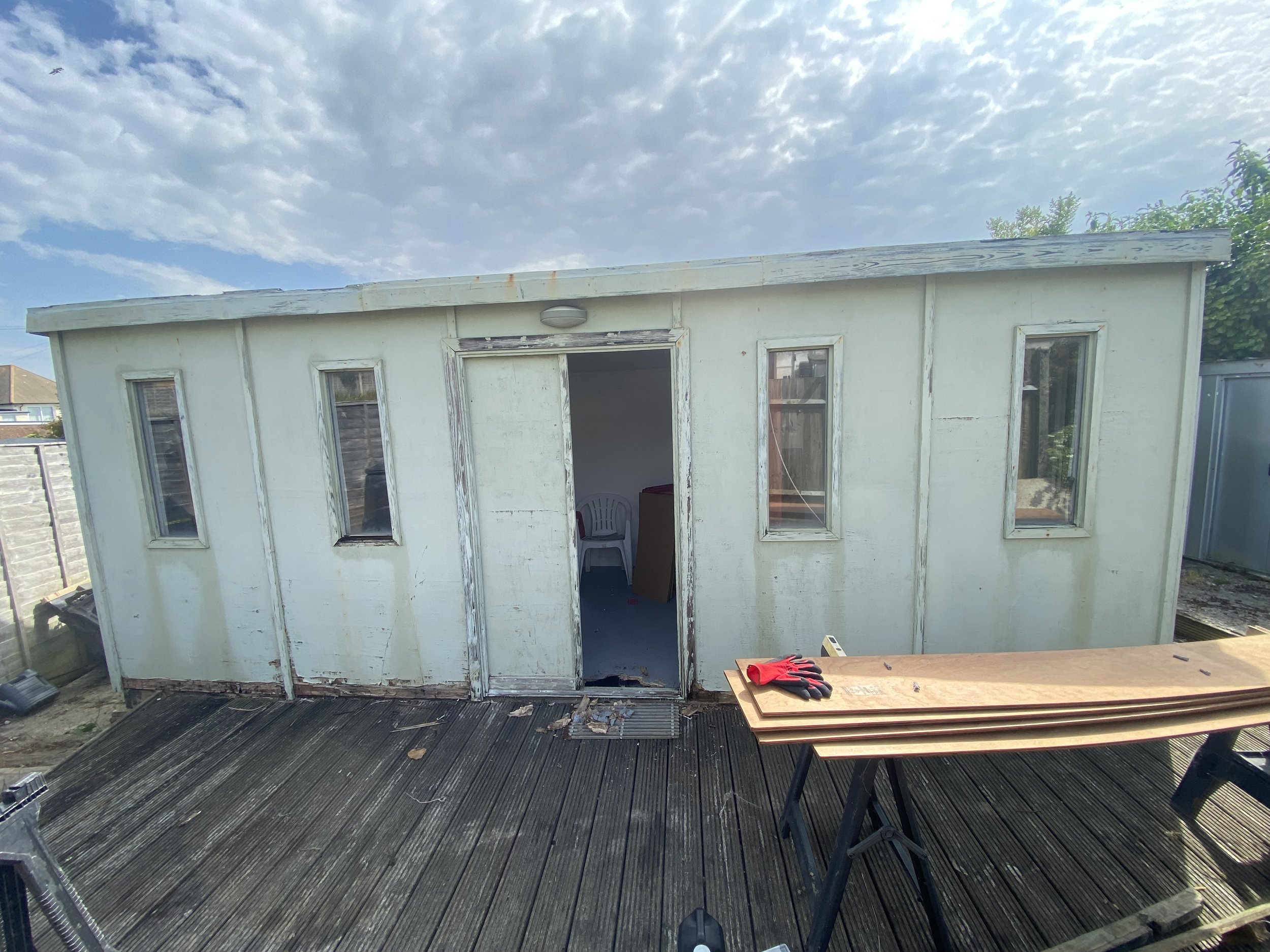
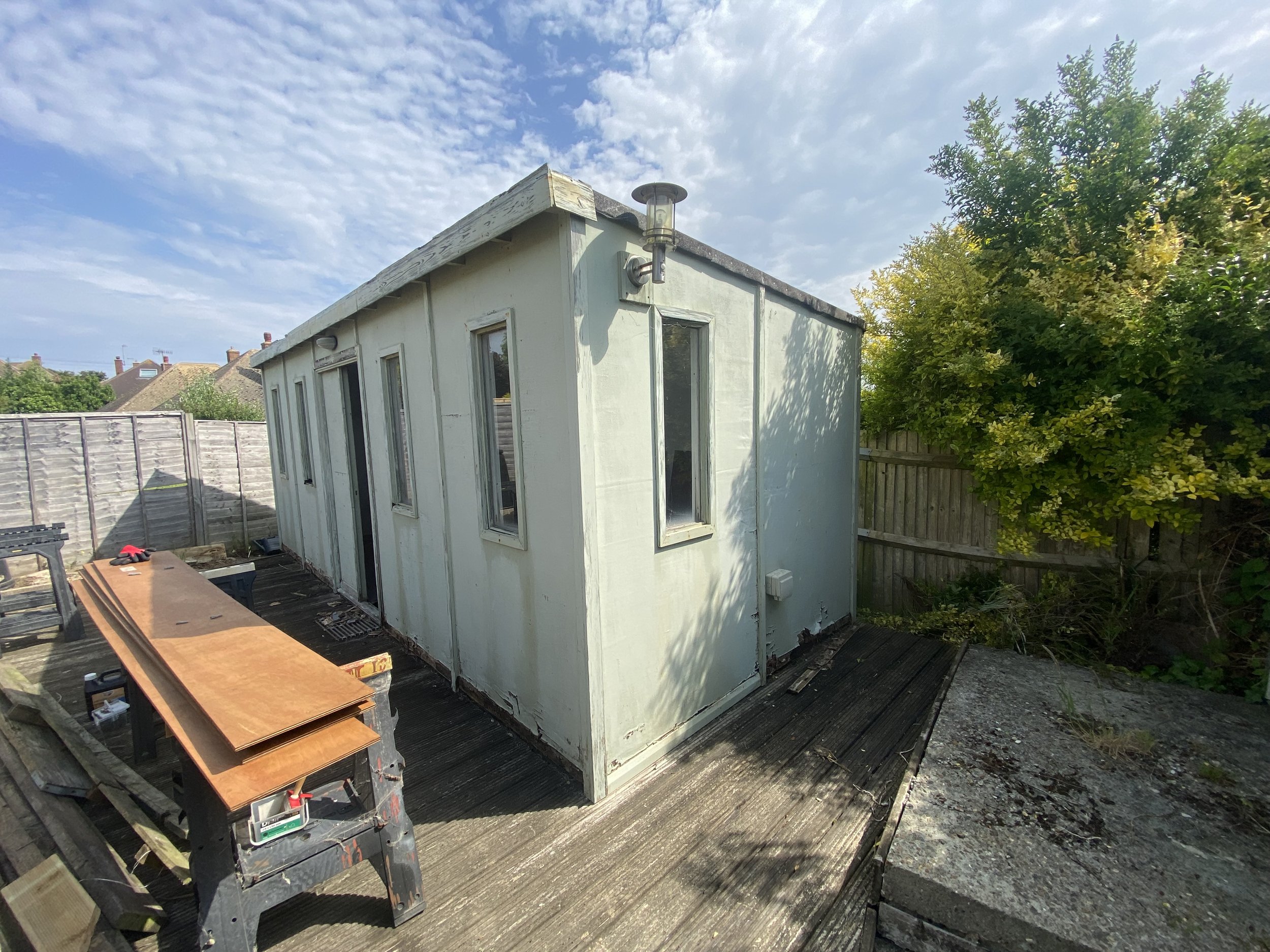
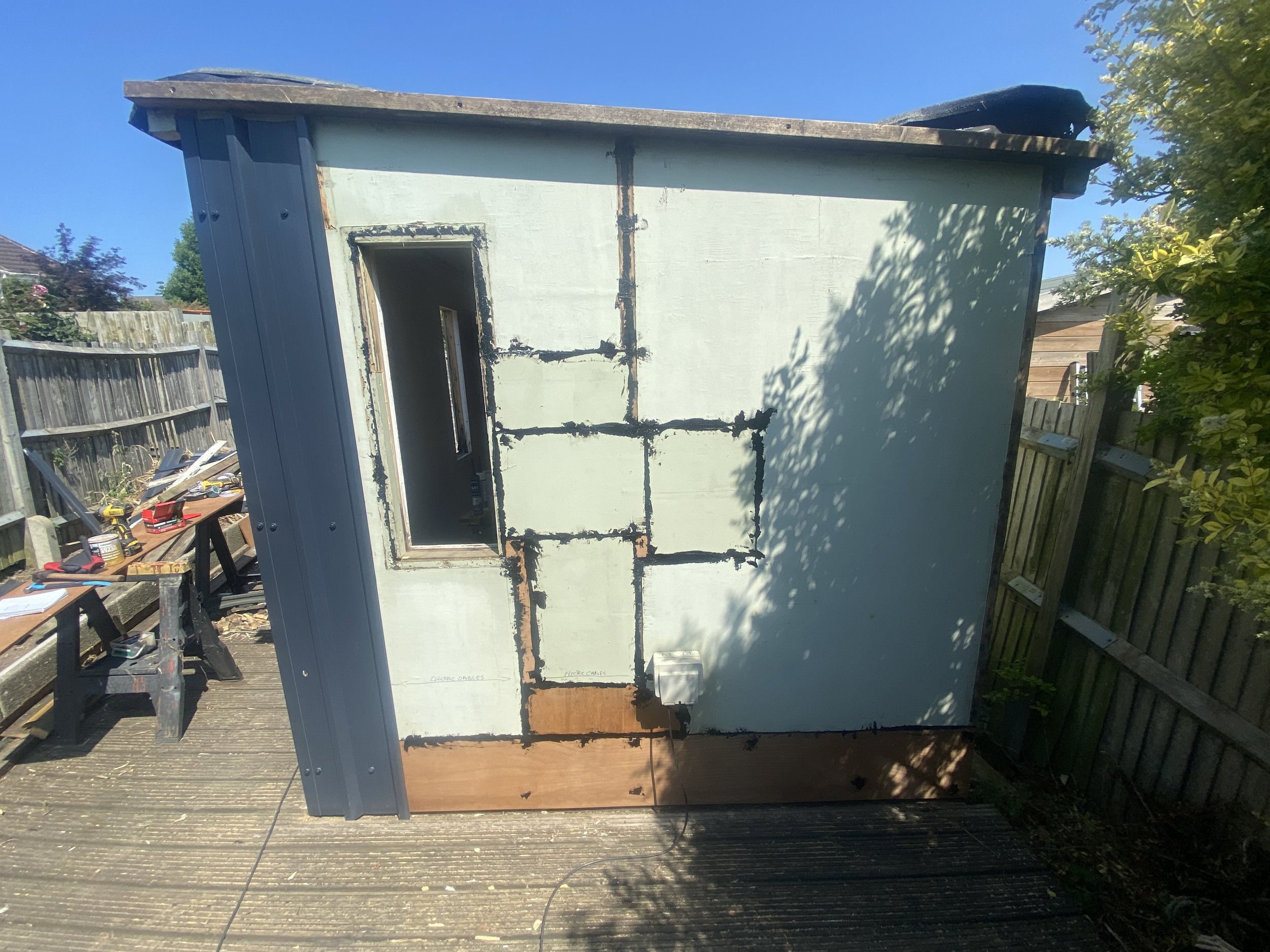
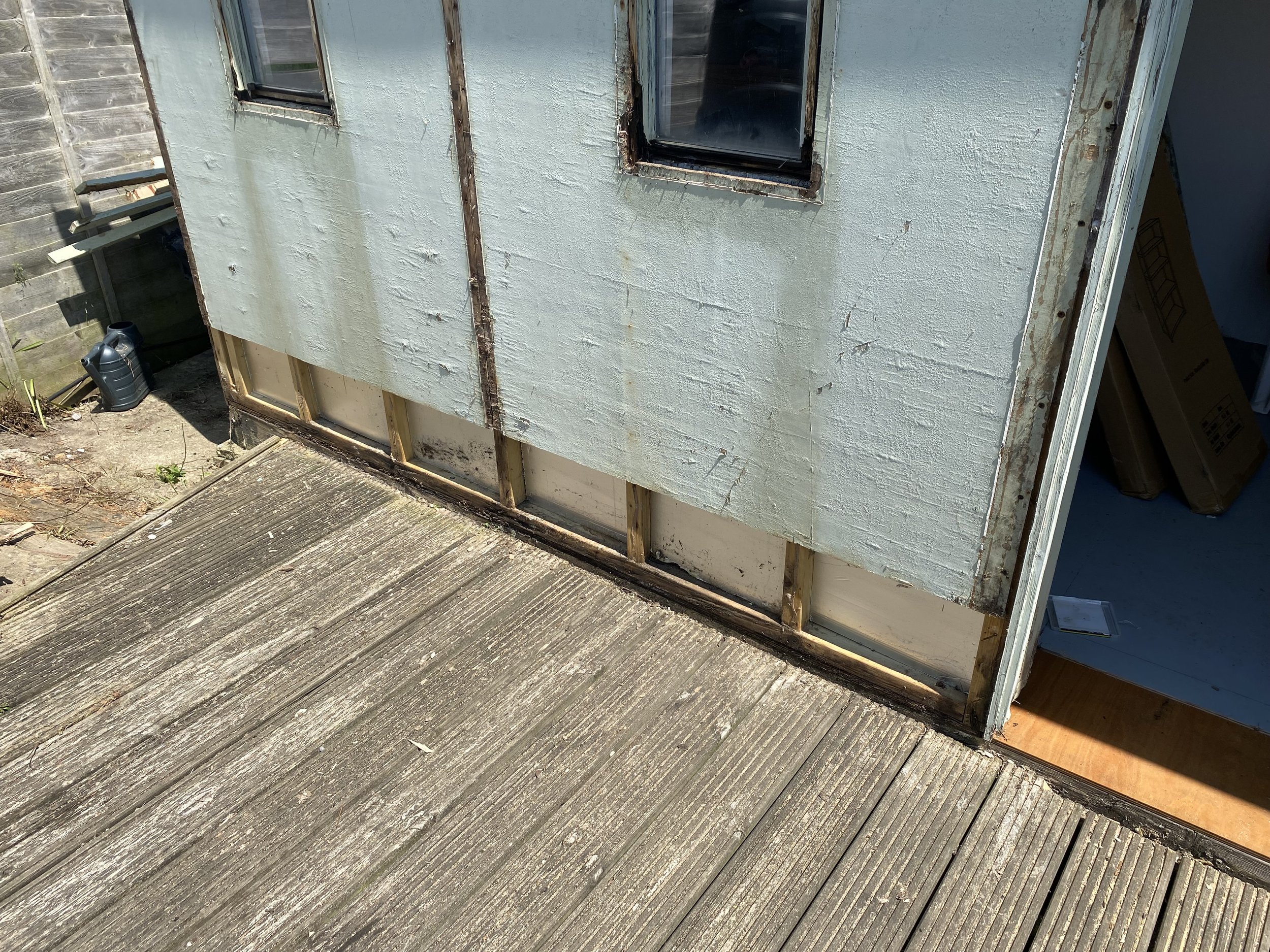

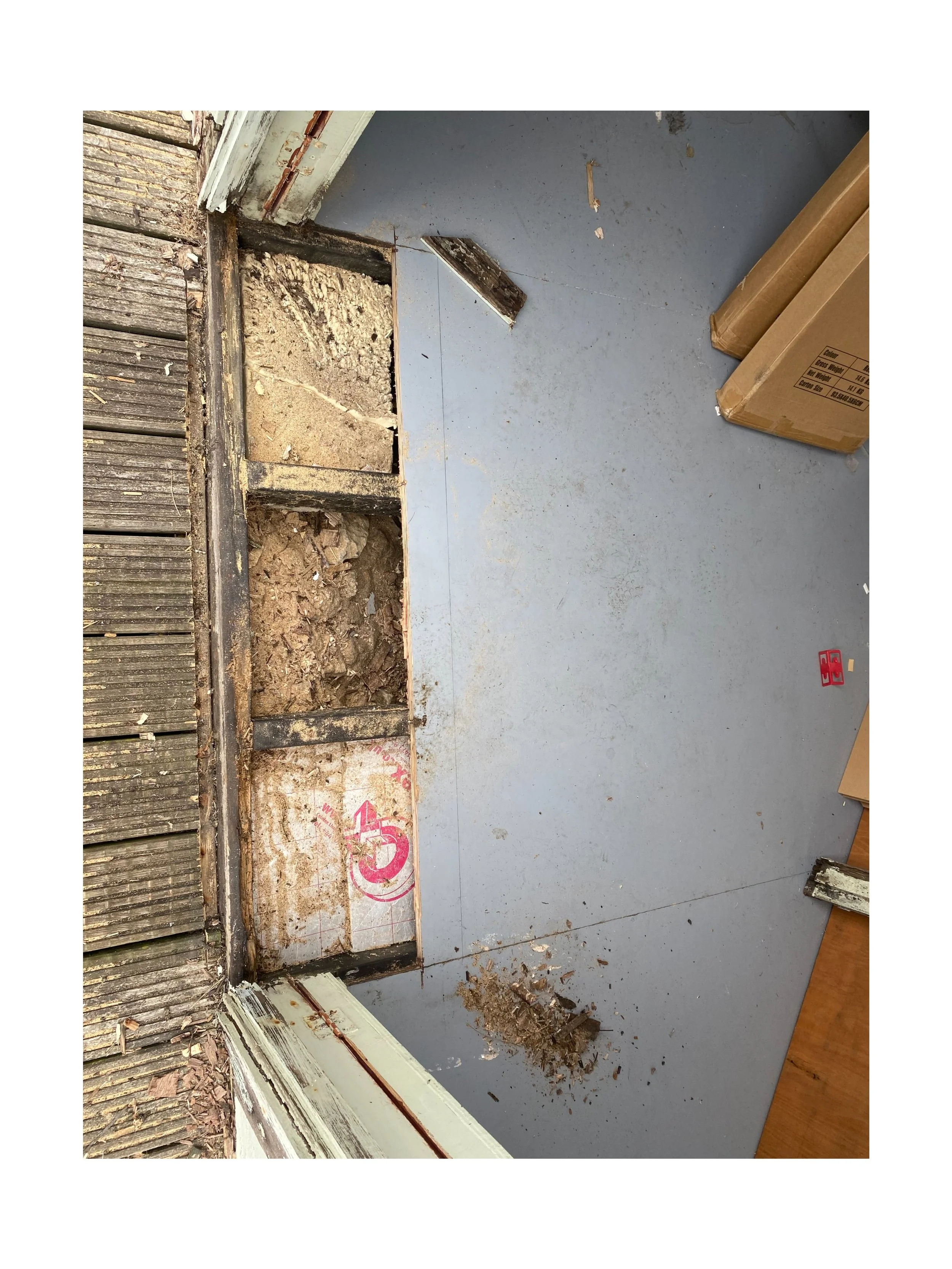
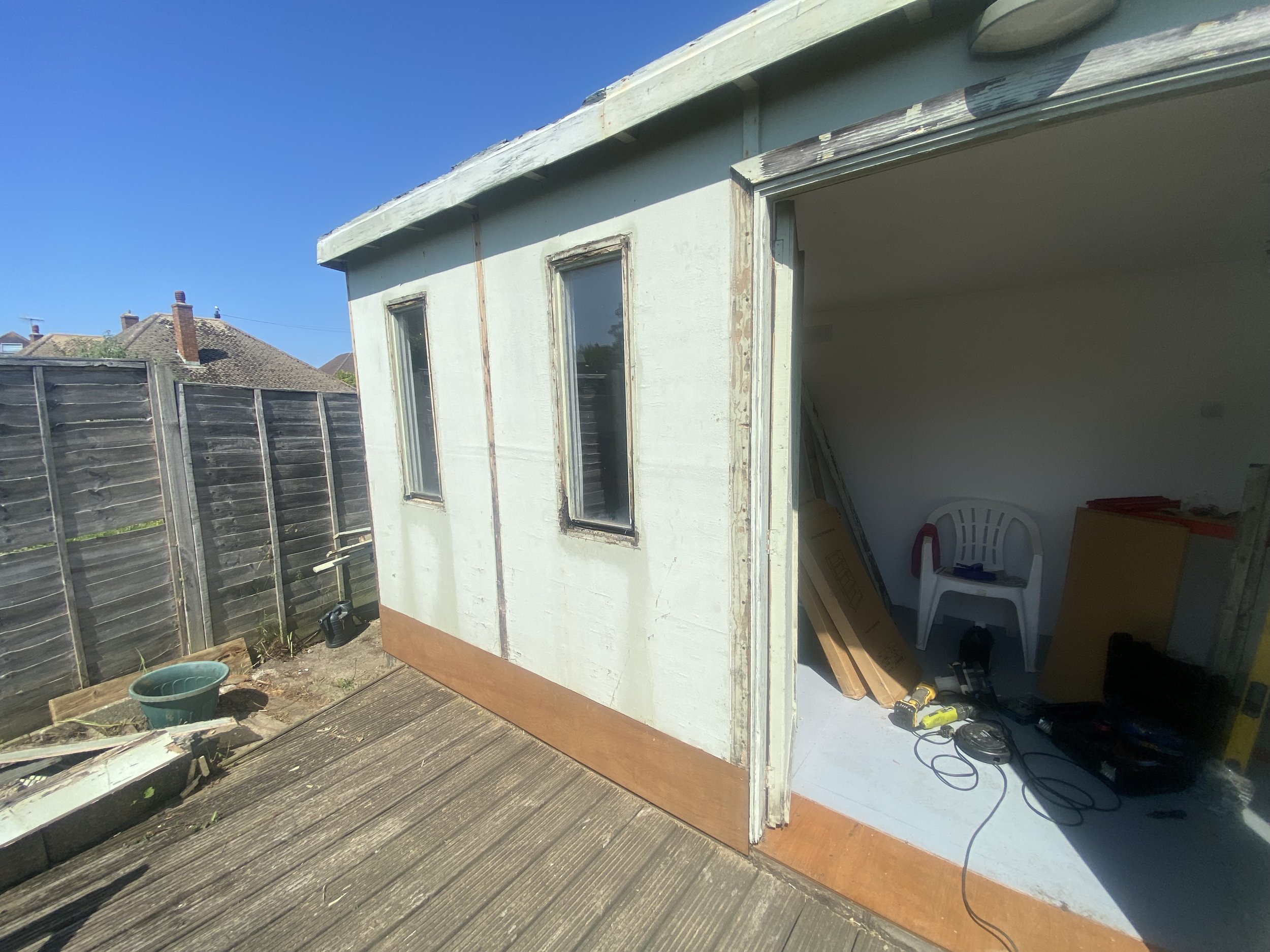
A garden office overhaul June/July 2025
The Existing Structure:
The garden office was built several years ago with a custom design. However, the outside was made from regular plywood, which is not suitable for outdoor use. It has badly deteriorated, with much of the structure and window frames rotting, letting water in and damaging the floor and walls inside.
Design Brief:
The owner wanted essential repairs while keeping most of the existing structure and reusing timber to save money. We discussed waterproofing options, and he chose box profile coated aluminium sheets for cladding. He also asked to replace damaged exterior ply with regular ply instead of marine ply to cut costs. The owner planned to repaint the interior after the work was done.
Issues to be resolved:
Bottom section of two sides of the plywood clad building abutted by decking rotten
Right side elevation of the building significantly rotten as it took the brunt of the weather
Five window surrounds each had varying degrees of water damaged
Water damage and rot to the bottom of both external doors and door threshold
Two vents in rear wall of structure had plastic cover glued over
Section of interior floor at entry way dangerously rotten
Other section of floor rotten
Water damage staining on interior walls
Two outside lights don't work because of incorrect wiring. One light above the door would have to stay on all the time for the security light on the side to work. The owner chose to have both lights removed.
Solutions and tasks completed:
trim edge of all decking boards abutting the exterior ply walls to reduce risk of transfer of water from one to the other
cut away bottom sections of the exterior ply walls and rotten sections of end elevation ply wall
replace cut away sections with new plywood that had been treated with Bartoline Creocote wood treatment and the edges painted with Everbuild 90101 Black Jack Bitumen Paint
remove window panes and repair window surrounds where necessary
removed both external light fixtures and wiring disconnected from the circuit and cut back so it could not be reconnected.
install Slate Blue 32/1000 Box Profile Sheeting 0.5 Thick Polyester paint coated aluminium sheet cladding to exterior walls
install Slate Blue 50mm x 50mm 90 Degree External Corner aluminium flashing with Polyester Paint Coating to all four corners to finish
remove two old air vents and replace with new louvre vents with integrated insect screens
use the same corner flashing to fashion water tight external window surround, window sill, door surround and frame around air vents
apply Bostik Pro S41 Window & Door Frame Silicone in Anthracite to door, window and air vent surrounds as necessary to ensure water tight
install ‘soffit’ to front elevation using left over timber and paint with Everbuild 90101 Black Jack Bitumen Paint
extend existing roof to both end elevations using reclaimed timber to give sufficient overlap to cladding. Paint this timber with Everbuild 90110 Black Jack Bitumen Paint
install new roof using covering using Roof Pro Black Premium Shed Felt which has a 15 year manufacturers guarantee
cut away two sections of interior floor and replace with new plywood treated with Bartoline Creocote wood treatment and the edges painted with Everbuild 90110 Black Jack Bitumen Paint. Top coat of floor paint to match existing flooring
create new door threshold using reclaimed timber, aluminium cladding and aluminium L-shape angle profile to stop future water ingress when doors are closed
paint interior walls, ceilings and around windows where water damage staining could be seen with Zinsser Cover Stain Primer, Sealer & Stain Killer. Making ready for customer to apply top coat himself
I hope you’ll agree with the owner that the end result looks brilliant!